Schneider Electric
Recycling
Closed-loop
Source
Post-production
Industry
Electronics
Material
SEBS/PP
“We’re extremely satisfied with the consistent purity Trebo is able to deliver, enabling us to send scrap back into our production without compromising any quality measures”
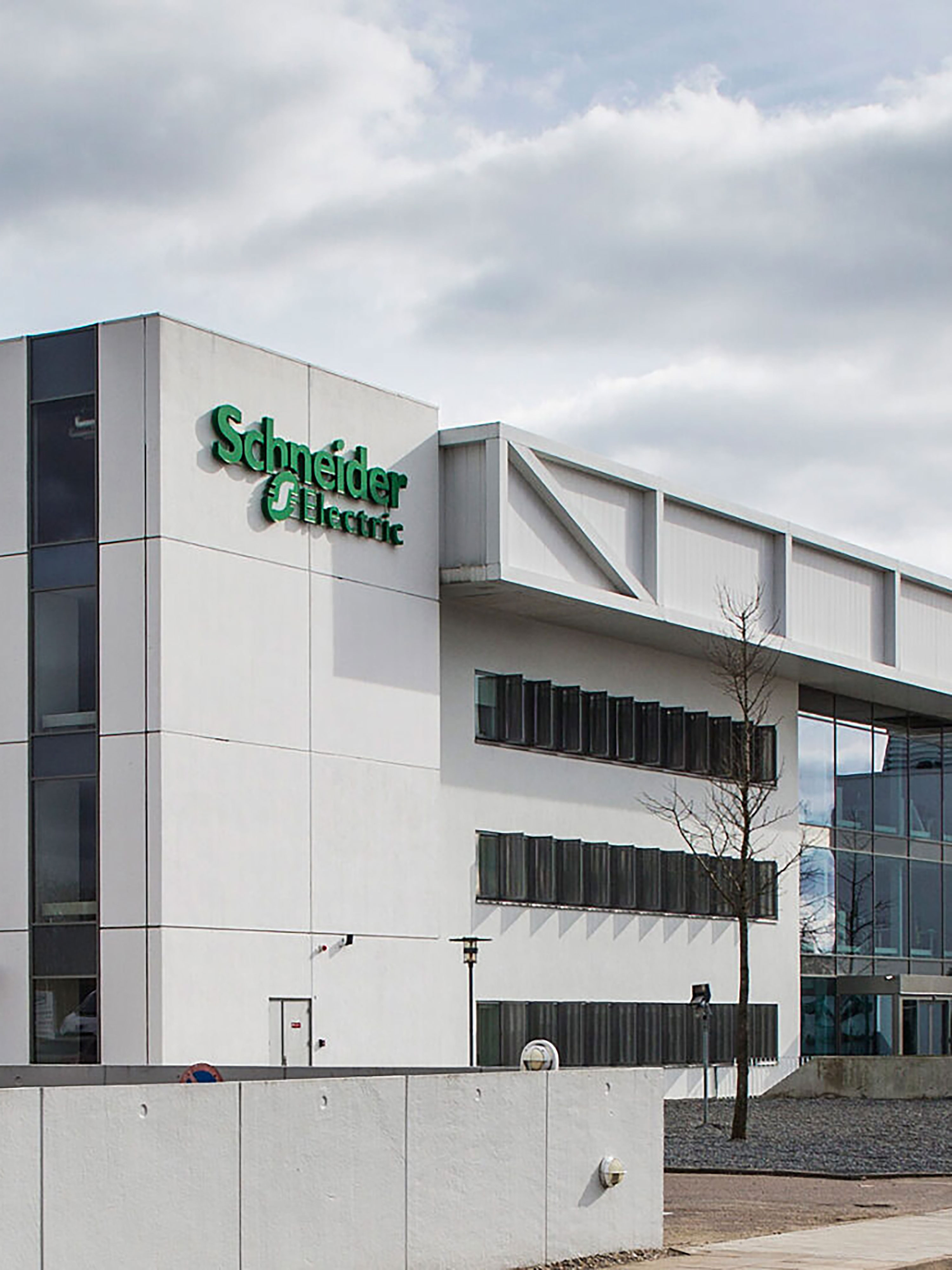
Background
Global electronics company and green transition front-runner, Schneider Electric, is set on applying circularity principles across their supply chain. As part of their sustainable efforts, they’ve teamed with us to make sure production scrap at their plant in Denmark is brought back in the loop for further usage.
One of our tasks is sorting a complicated waste stream of inlets and rejects in SEBS and PP that derives from co-injection moulding components for a major line of electrical equipment. Due to the low tolerance margins of Schneider Electric’s highly engineered products, an extremely high purity of the sorted content is needed for it to be reutilised in new manufacturing processes.
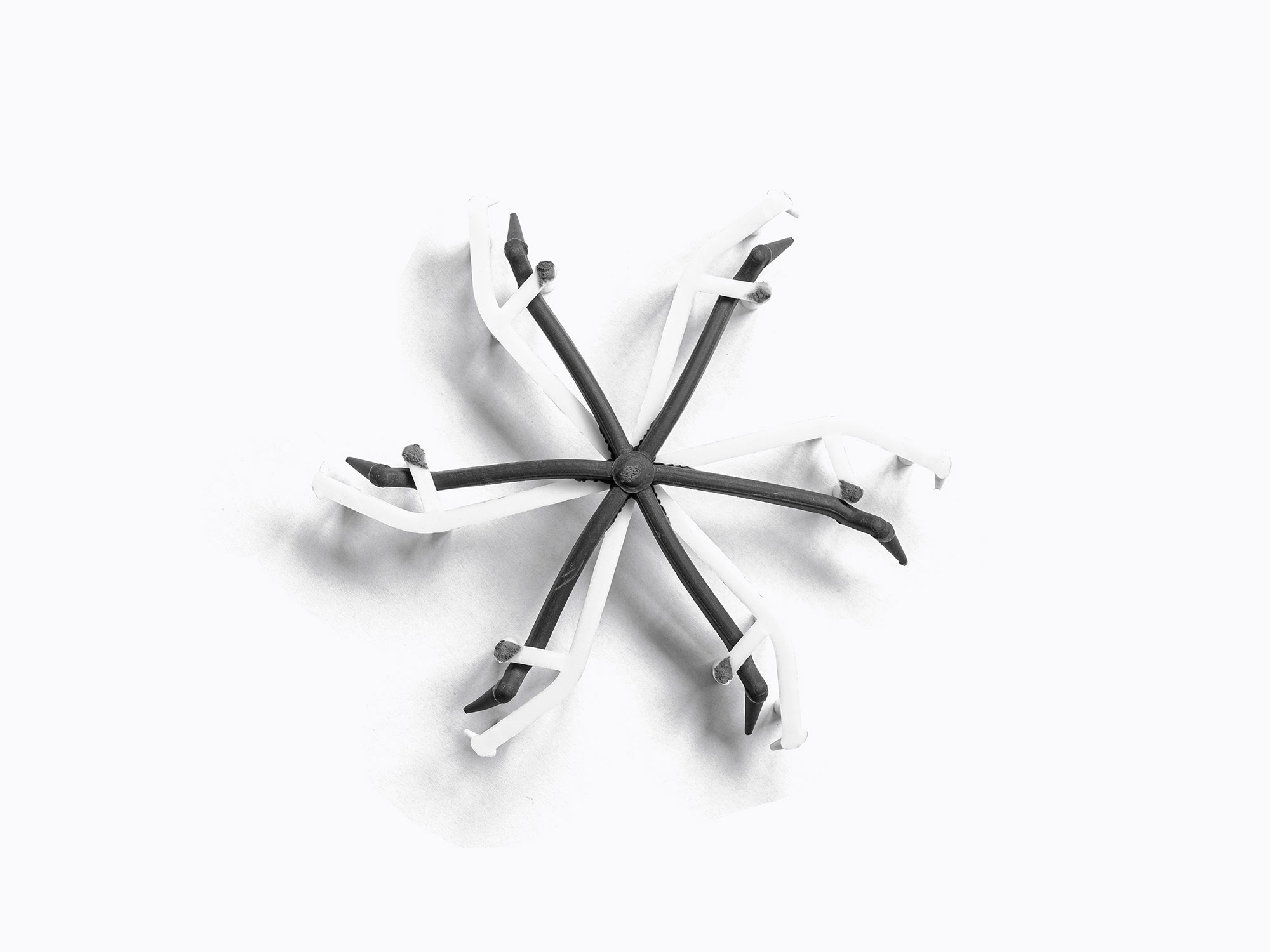
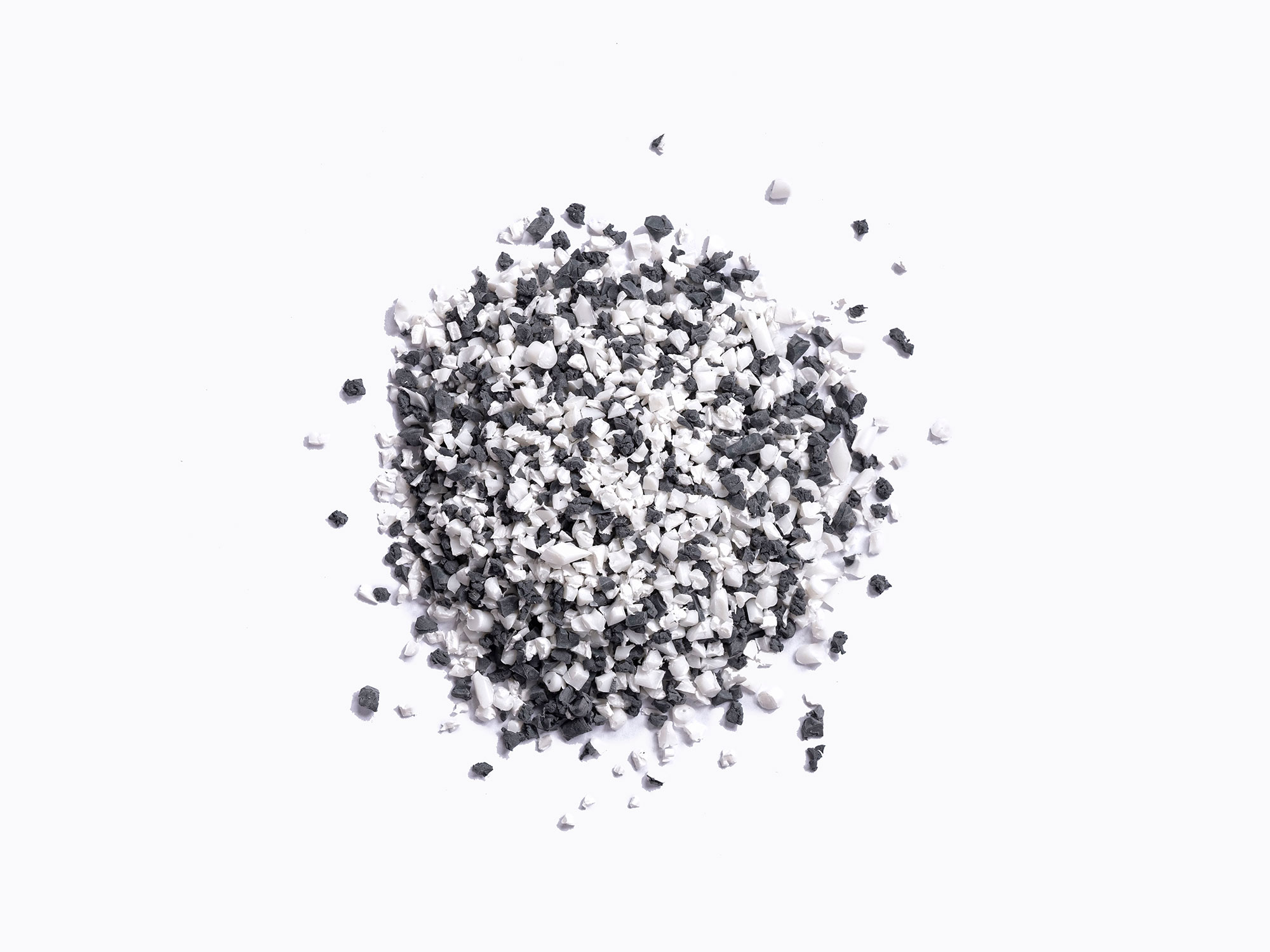
Outcome
This is how our partnership works. Schneider Electric collects the scrap, shreds it into flakes, and delivers it to our factory when they have enough to fill a full truck. Using our patented system, we sort the plastics mixture into pure fractions of the black SEBS and white PP, pack it and ship it back to Schneider Electric’s plant.
Meeting the demanding sorting requirements, yielding super-clean SEBS and PP, Schneider Electric are able to produce new items using reclaimed materials from previous productions. The line of electrical equipment is now made of 50% secondary raw material and 50% virgin raw material securing a durable balance in the flow of materials.
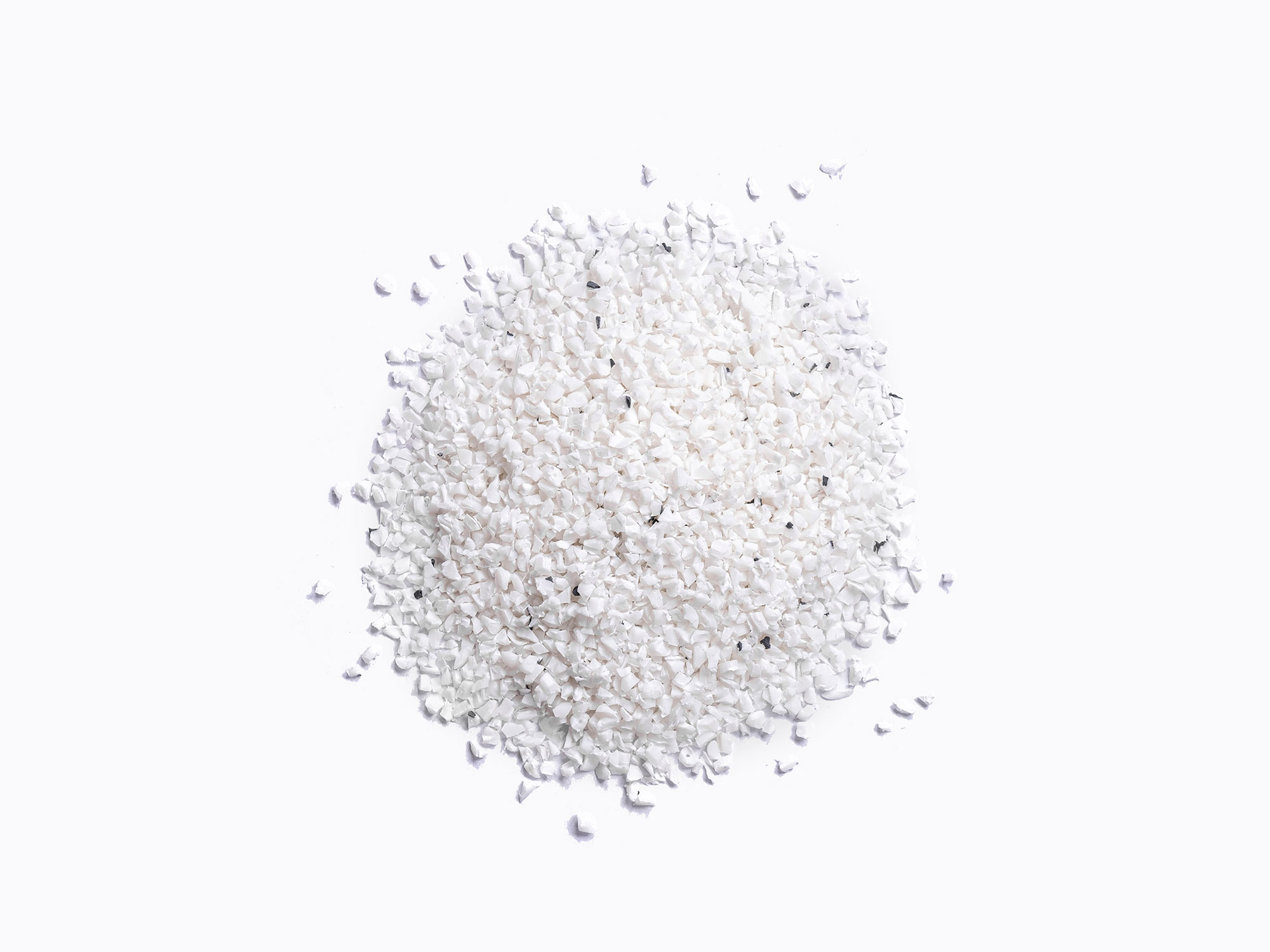
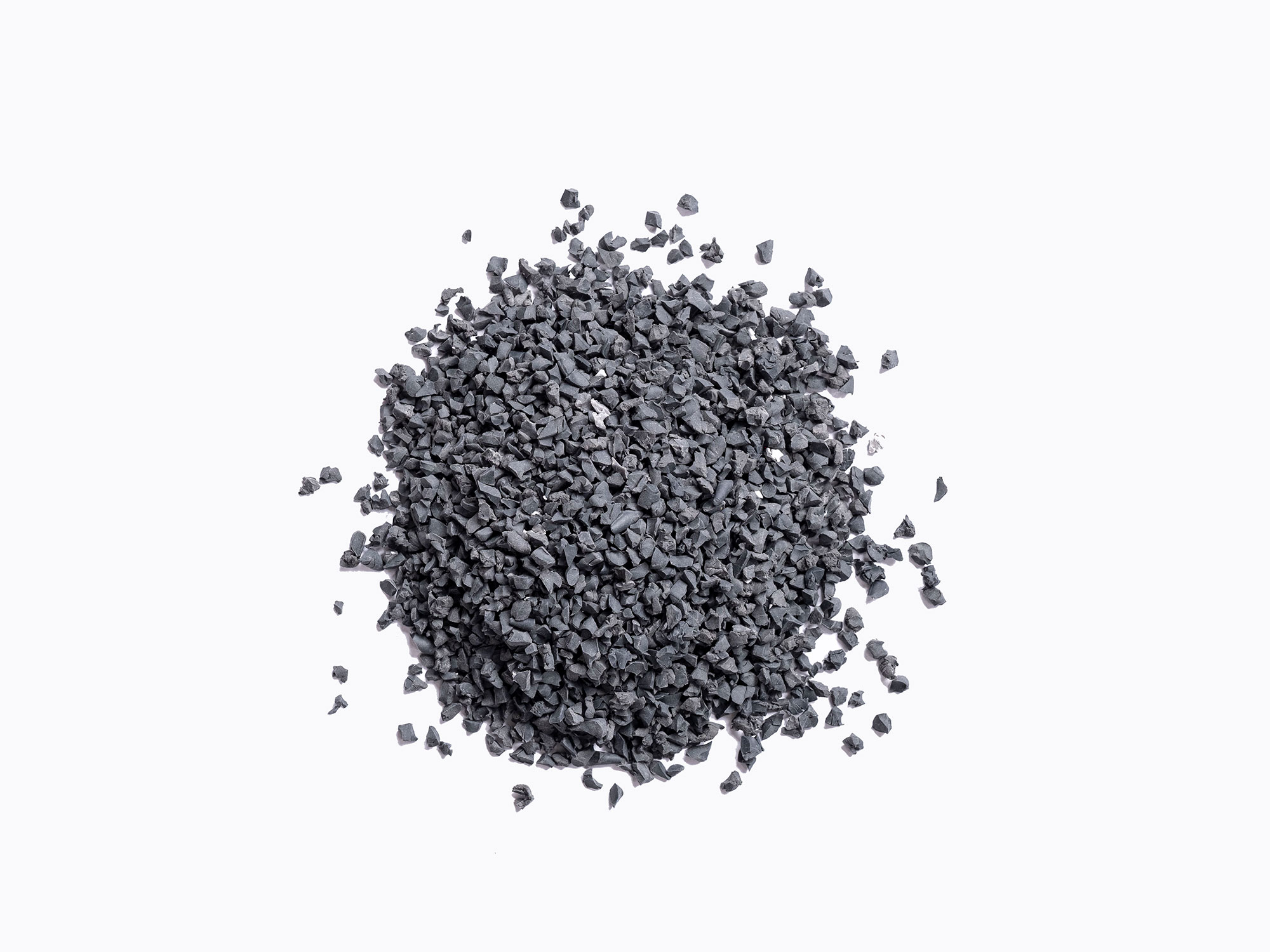
Benefits
Here’s some of the advantages Schneider Electric has gained by sorting their scrap for closed-loop recycling via our service.
95% recycling boost
Now 95% of the post-production waste is recycled into the same process that generated it.
50% savings on input
With two new streams of quality secondary raw material, the need for virgin plastics is 50% lower.
+30,000 kg CO2 saved
By recycling the production scrap in a closed-loop at least 30,000 kg CO2 a year is saved.
No extra operating costs
With seamless integration, the new recycling initiative does not cause additional operating costs.